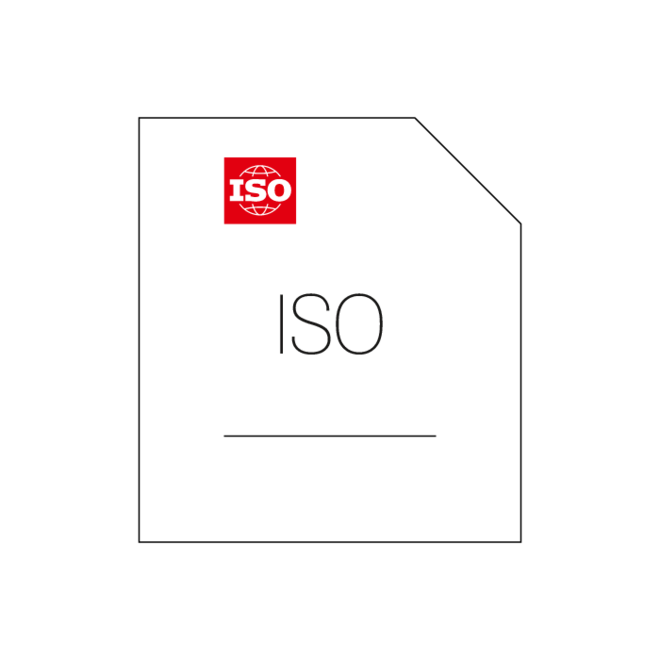
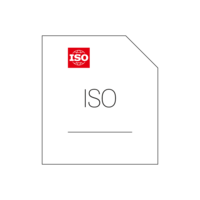
ISO 13919-1:2019
Issue date: 2019 10 25
Electron and laser-beam welded joints — Requirements and recommendations on quality levels for imperfections — Part 1: Steel, nickel, titanium and their alloys
This document gives requirements and recommendations on levels of imperfections in electron and laser-beam welded joints in steel, nickel, titanium and their alloys. Three levels are given in such a way as to permit application for a wide range of welded fabrications. Quality level B corresponds to the highest requirement of the finished weld. The levels refer to production quality and not to the fitness-for-purpose of the product manufactured.
This document applies to electron and laser beam welding of:
— steel, nickel, titanium and their alloys;
— all types of welds welded with or without additional filler wire;
— materials equal to or above 0,5 mm thickness for electron and laser beam welding.
The purpose of this document is to define the dimensions of typical imperfections which can be expected in normal fabrication. It can be used within a quality system for the production of welded joints. It provides three sets of dimensional values from which a selection can be made for a particular application. The quality level necessary in each case is defined by the application standard or the responsible designer in conjunction with the manufacturer, user and/or other parties concerned. The quality level is expected to be prescribed prior to the start of production, preferably at the enquiry or order stage. For special purposes, additional details may need to be prescribed.
When significant deviations from the joint geometries and dimensions stated in this document are present in the welded product, it is necessary to evaluate to what extent the provisions of this document can apply.
Metallurgical aspects, e.g. grain size, hardness are not covered by this document.
This document does not address the methods used for the detection of imperfections. This document is directly applicable to visual examination of welds and does not include details of recommended methods of detection or sizing by other non-destructive means. There are difficulties in using these limits to establish appropriate criteria applicable to non-destructive testing methods, such as ultrasonic, radiographic and penetrant testing, and they can need to be supplemented by additional requirements for inspection, examination and testing.